Master Process Control Systems Including SCADA and More
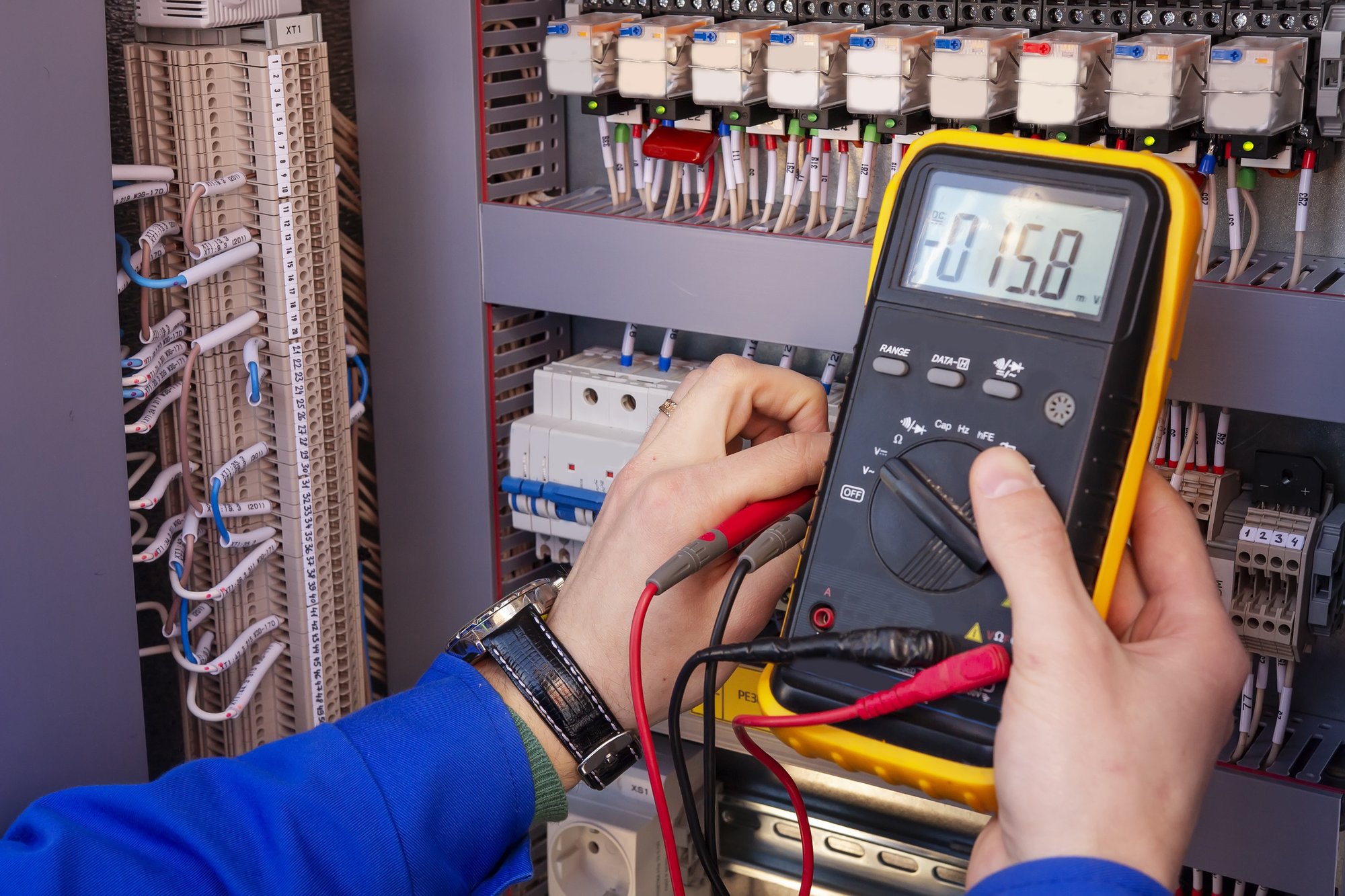
Hands-On Training, Real-World Skills, and Industry-Proven Expertise
At Adaptive Training Services (ATS), we understand the critical role process control plays in ensuring efficient and reliable industrial operations. That's why we've partnered with Amatrol, the industry leader in industrial training solutions, to offer a comprehensive process control training curriculum designed to equip your team with the skills they need to succeed.
Our Process Control Training Curriculum
Our process control training program covers a wide range of essential topics, including:
-
Process Control Systems: Understand the different types of process control systems, including level and flow, temperature, analytical, and pressure.
-
Process Control Fundamentals: Learn the principles of process control, including feedback control, feedforward control, and cascade control.
-
Instrumentation and Sensors: Gain expertise in various process control instruments and sensors, such as transmitters, controllers, and actuators.
-
SCADA Systems: Master the use of SCADA systems to monitor and control industrial processes.
-
Troubleshooting and Maintenance: Develop the skills to diagnose and repair process control equipment effectively.
Why Choose ATS?
- Hands-On Learning: Our labs are equipped with state-of-the-art process control equipment, providing your employees with practical experience.
- Industry-Proven Curriculum: We leverage Amatrol's renowned process control training programs to ensure your team receives the most up-to-date and relevant knowledge.
- Experienced Instructors: Our trainers have a wealth of experience in the process control industry, providing expert guidance and support.
- Flexible Delivery: We offer various training formats to fit your team's schedule and learning preferences.
- Measurable Results: We track your team's progress and provide detailed reports to assess their knowledge and skill development.

Invest in Your Team's Future
By investing in ATS's process control training, you're not just improving your employees' skills; you're also:
- Enhancing Efficiency: Well-trained process control technicians can optimize system performance and reduce downtime.
- Improving Quality: Ensure consistent and reliable product quality through effective process control.
- Reducing Costs: Prevent costly equipment failures and minimize energy consumption.
- Attracting Top Talent: A commitment to training and development can help you attract and retain skilled process control technicians.
Ready to Get Started?
Contact us today to learn more about our process control training programs and schedule a consultation. Let us help you build a more skilled, efficient, and reliable process control team.
Frequently Asked Questions
What is a PID controller and how does it work?
A Proportional-Integral-Derivative (PID) controller is a type of feedback controller commonly used in process control systems. It uses three control modes: proportional, integral, and derivative, to regulate a process variable to a desired setpoint. The proportional mode adjusts the output based on the error between the setpoint and the process variable. The integral mode corrects for steady-state errors, and the derivative mode anticipates future changes in the process variable.
What is SCADA and how is it used in process control?
SCADA stands for Supervisory Control and Data Acquisition. It is a system that allows operators to monitor and control industrial processes from a central location. SCADA systems use sensors and other devices to collect data from the field and present it to operators in a user-friendly interface. Operators can then use SCADA systems to make adjustments to the process as needed.
What is the difference between open-loop and closed-loop control?
In open-loop control, the output of a process is not measured or feedback to the controller. This means that the controller has no way of knowing whether the process variable has reached the desired setpoint. In closed-loop control, the output of the process is measured and feedback to the controller. This allows the controller to adjust the input to the process in order to maintain the desired setpoint.